Time, quality and price are the three core values which are to be managed proficiently by every company irrespective of the goods or services it is producing. Whenever a client chooses to buy something, these are their three pillars.
They either want a reasonable price, quick delivery or excellent quality. We all know that there is no technology with which all of these three values can be provided in a single product simultaneously. But clients can expect that they will get two out these three values at their best.
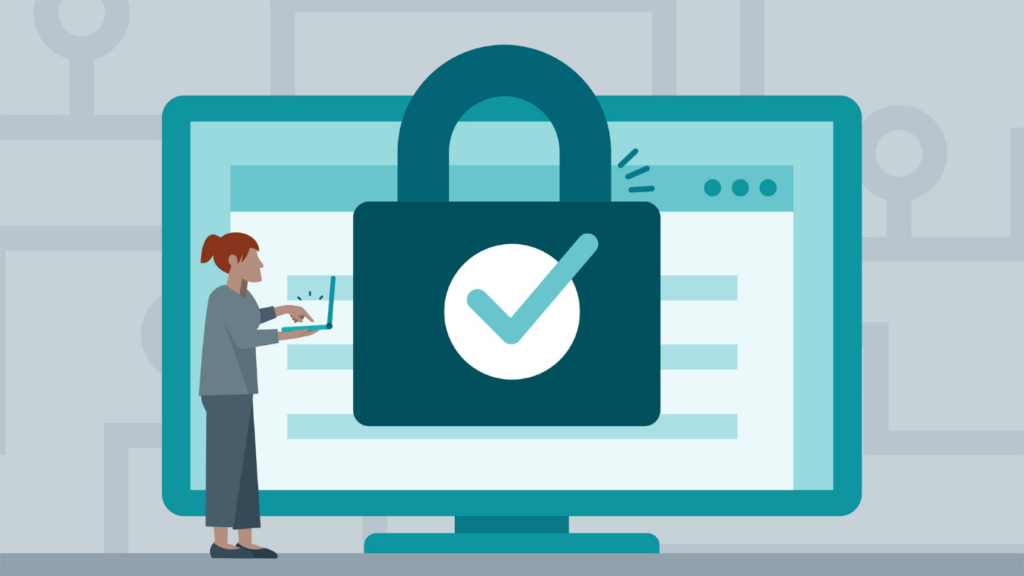
When customers are asked which is the most important for them and most of them usually answers quality. In this blog, we are focussing on the software quality and the way one can support and achieve it during the development process.
Factors for software quality
A software product to be considered as a high-grade product should adhere to a range of requirements. Here are some essential quality factors that are to be considered:
Usability: a clear and simple interface
Performance: the capability to do transactions under a determined workload with the sufficient workload
Extensibility: the capability of adding functions to an existing system without doing any kind of damage
Security: the ability to safeguard personal data through authentication and authorization techniques.
How can someone control software quality? Quality control and quality assurance are the two practices which the producers utilize to maintain and improve the quality of their services and products.
Many people wonder whether there is a difference between quality assurance, planning, and control or not. This confusion is the result of similar-sounding terms. Although quality assurance is an integrated effort which includes the below-mentioned activities:
- Analyzing
- Planning
- Implementation
- Control
- Correction
Therefore, control and planning are important parts of the general QA process.
The difference between quality control solution and assurance is one of the most frequently asked. This is because these two terms are often confused. It is crucial to understand that are not synonymous but part of a single management system.
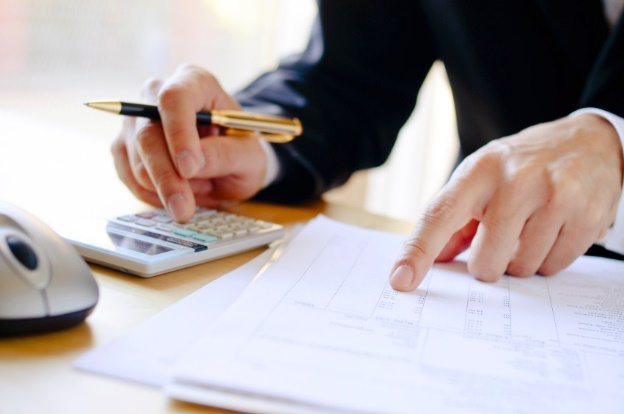
They have much different and cannot be used in place of each other. If you are clear about the differences between them then it will be helpful for you to accurately distribute duties among your team members, create an efficient management plan and ensure that the final product meets the defined needs and standards.
Quality Assurance
Before the beginning of a production, QA activities are well-determined. These activities are conducted from the starting of the projects and continuous during the whole project. These processes make sure that all agree to approaches, methods and techniques are followed without any kind of negligence so that the errors are prevented and as a consequence, satisfy the needs of the customers.
The objective of QA is to arrange a flawless development and protect the end product from all kinds of possible defects. “Zero defect” approach is usually followed under QA processes.
What are the examples of QA?
- Project planning
- Creating standards
- External and internal audits
- Process analysis
- Selection of tracking tools
- Process documentation
- Checklist inspection
- Process documentation
- Training courses for team members
Pros of Quality assurance
The advantages of quality assurance are important:
- There is a significant reduction in the final cost as the mistakes are prevented at an early stage through QA, so no resources or efforts are invested into reworking on them at a later stage.
- There is a noticeable enhancement in the motivation of the employees who are now getting recognition for their efforts and they understand their importance. This will provide better outcomes.
- No barriers between manager and workers
Cons of Quality Assurance:
- High initial cost
- It is a time-consuming process wherein you invest a lot of time in training your staff for QA.
Quality Control
Unlike QA which is dealt with production, QC is concerned with output. Verification of deliverables and detecting the mistakes are the two most crucial functions of this process. This does not let any kind of defective solution to reach a customer.
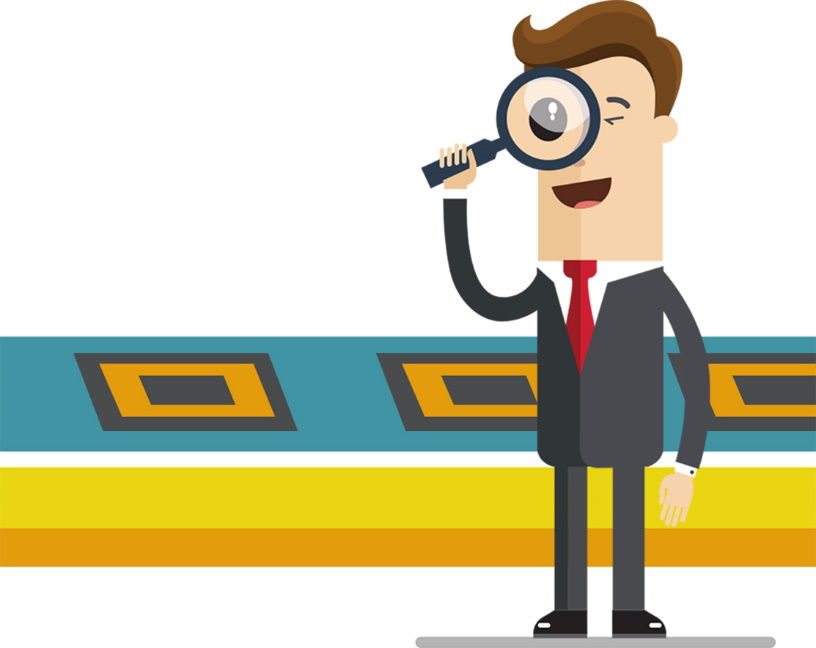
It ensures that the end product is adhering to the expectations of the customers and meets the predefined standards. In other words, QC can be referred to as the checkpoint prior to the delivery of a final product. Let’s discuss the various advantages and disadvantages of Quality Control.
Also Read: Contract Management Solution
Pros:
- Significant decrease in consumer complaints after the final delivery of the goods.
- Less cost
- Improves the performance
Cons:
- Delays the delivery
- More human resources required
Conclusion:
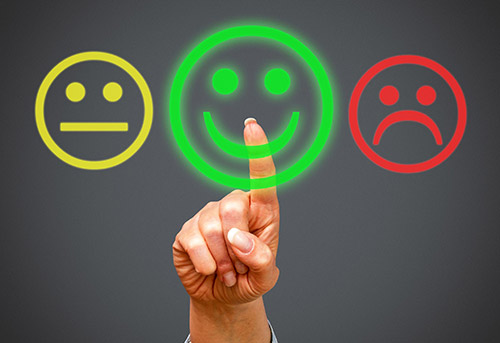
Every business knows that quality is something that attracts the customers with utmost power. Furthermore, it increases sales. The two practices; QA and QC are crucial to create and maintain end products of fine quality. Although they are different but coupled which cannot be ignored by any company. Nowadays, more and more companies are choosing quality inspection services from reputed companies in India for this purpose. You can also avail this service to make your QA/QC tasks easy.